Dewatering is the process of removing liquids from sludge slurry, typically employing one of three main techniques: plate and frame filter press, centrifuge, and belt press. These methods are utilized in wastewater treatment plants, power plants, refineries, and drinking water facilities to reduce the sludge volume, thereby making transportation more cost-effective.
Depending on specific conditions, one of the following dewatering methods can be applied:
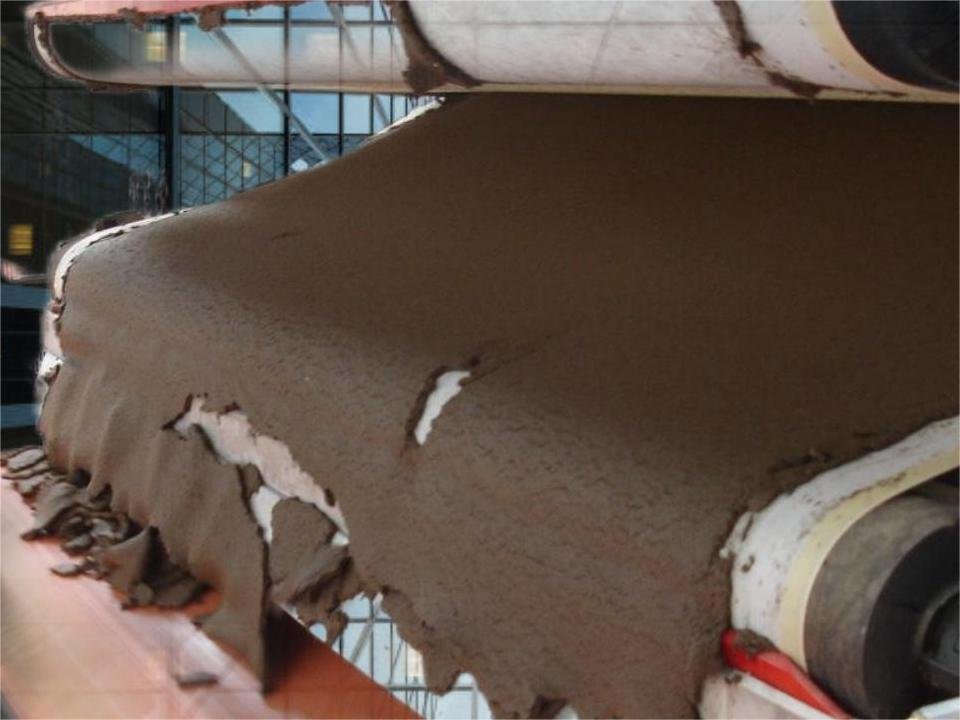
Plate and Frame Filter Press
Plate and frame filter presses use recessed-chamber filter plates to separate liquids from solids. Two plates form a chamber to pressurize the slurry, squeezing out the filtrate through a filter cloth lining. The filter cake, which is between 40% and 70% solids by weight, is collected on the surface of the filter plate cloths and dropped onto a horizontal conveyor. This method is highly effective, producing the highest content of solid material, making transportation and disposal more cost-effective. Additionally, operating a plate and frame filter press does not require special licensing, and the solids produced are stackable and economical to transport
Centrifuge
A centrifuge separates components of different densities by employing high rotational speeds. The principle is based on buoyancy, where higher density components fall to the bottom of the mixture, and less dense components remain suspended. Centrifuges typically produce solids with a content of 25% to 35% by weight. The primary advantage of this method is its speed, making it ideal for situations prioritizing oil recovery over the quality of residual solids.
Belt Filter Press
The belt filter press is used when high-moisture content in the filter cake is acceptable. It produces solids with a content of 18% to 25% by weight. As a continuous process, it is effective for high-volume waste streams where the production of low-quality filter cake is acceptable. This method is commonly employed in municipal wastewater treatment plants due to its efficiency in handling large volumes.
The above sludge dewatering processes require specific machinery. Faced with the increasing cost of sewage treatment, as a manufacturer of mining polymers, we can provide you with more effective products that can save labor and machinery costs. Let's take a look at how it works:
The Use of SOCO® Polymer Water-Absorbent Materials for Sediment and Sludge Dewatering
This method is an emerging and efficient technology that takes advantage of the strong water absorption capacity of these materials to quickly absorb and convert liquids in sludge into solids. It is suitable for a variety of environments requiring dewatering, including wastewater treatment plants, power plants, and drinking water facilities.
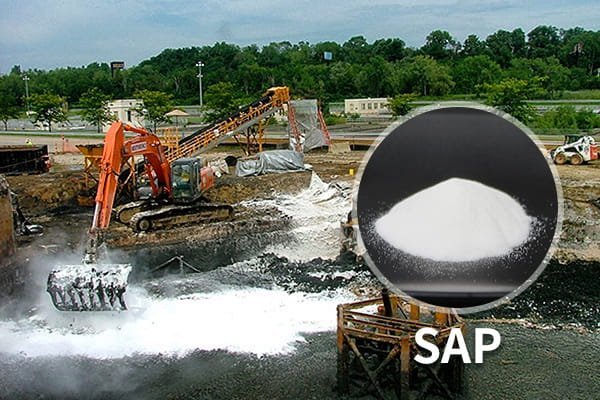
SOCO® Polymer water-absorbing materials can absorb and lock large amounts of moisture, converting liquids into gel-like solids. Through this process, sludge volume is significantly reduced, and the treated solids are easier to transport and handle.
SOCO® Polymer Action Steps
l Super absorbent materials are added to the sludge.
l The material quickly absorbs the moisture in the sludge and forms a solid gel.
l The dewatered solids are processed, transported, or further disposed of.
Cost Saving Ratio
Using polymer water-absorbing materials for dehydration can achieve cost savings in many aspects:
Transportation Cost: Polymer water-absorbing materials can significantly reduce sludge volume and reduce transportation requirements. The specific saving ratio depends on the initial moisture content and final solids content of the sludge, but it can usually reduce transportation costs by 30%-50%.
Processing Costs: By reducing sludge volume, subsequent treatment and disposal costs are reduced. Total processing cost savings are expected to be 20%-40%.
Operational Efficiency: The use of polymer water-absorbent materials simplifies the dehydration process, improves treatment efficiency, and reduces labor and equipment maintenance costs.
By using SOCO® Polymer water-absorbent materials for sediment and sludge dewatering, treatment efficiency can not only be improved, but transportation and disposal costs can also be significantly reduced. The specific cost saving ratio depends on the specific situation, but it is usually between 30% and 50%.
Localisation : No.51-2, Wuyang road , Qingdao, China, 266000 qingdao,
Personne à contacter : socochem polymer, +18 6 61 68 06 08